challenges with
coarse particle flotation
A critical component for achieving maximum mineral recovery in CPF systems is the control valve at the bottom of the flotation tanks. These valves must possess exceptional throttling response, optimal flow dynamics, reliability, and wear resistance. A specialized engineering approach is essential to designing valves robust enough to withstand the abrasive conditions inherent in flotation operations.
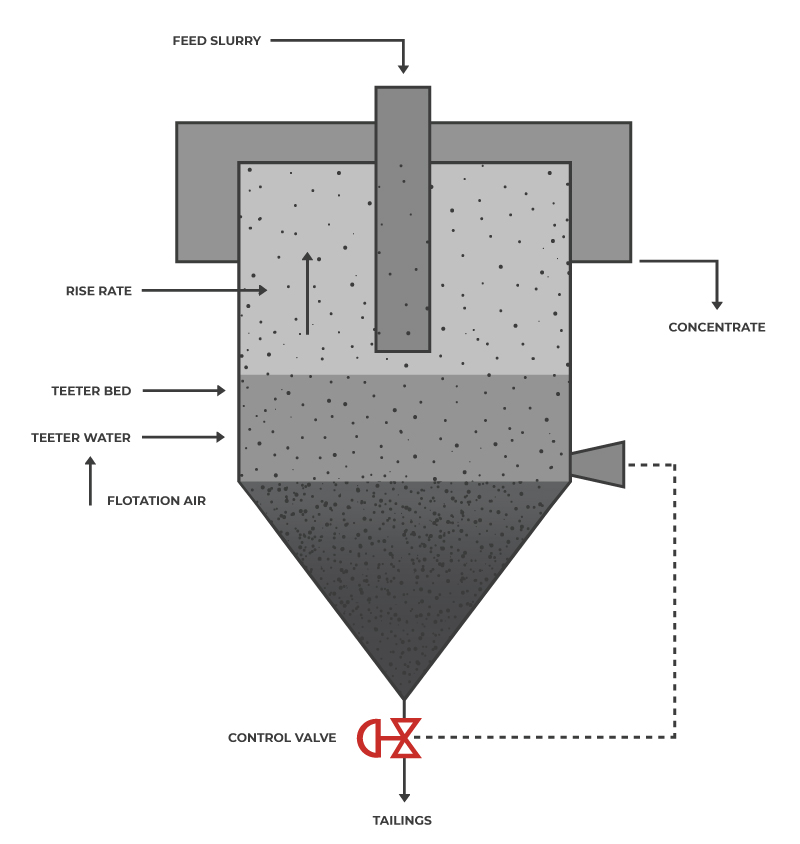